Global technology company ZF takes over completed facility in Park Ostrov North
ZF has officially taken over a newly completed facility in the Park Ostrov North industrial zone. The 57,400-square-metre facility was designed from the outset with sustainability principles in mind. The project was developed on one of the largest brownfield sites in Czechia by Panattoni, while the investment was provided by Accolade Group.
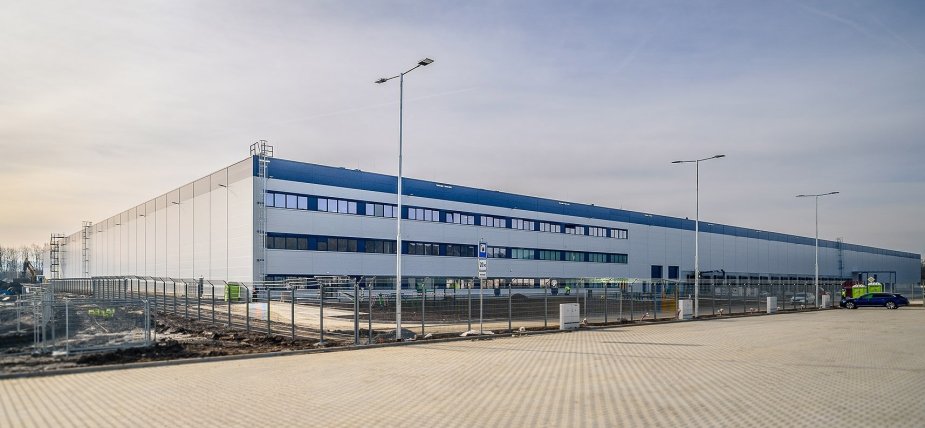
ZF is a leading global technology company supplying advanced products and systems for mobility in passenger cars, commercial vehicles and industrial applications. The company operates 162 manufacturing plants across 31 countries and employs approximately 168,700 people worldwide, including 3,500 in the Czech Republic, where it already operates R&D centres in Jablonec nad Nisou, Pilsen and Zlín, as well as manufacturing plants in Frýdlant, Jablonec nad Nisou, Klášterec nad Ohří, Staňkov, Stará Boleslav and Žatec.
In Ostrov, ZF has built a highly automated distribution centre for the aftermarket sector. Sustainability was a key priority from the very start of construction. The facility incorporates recycled and eco-friendly materials, ensures efficient waste management and minimizes single-use plastics. Additionally, it is powered by renewable energy, with optimized consumption through energy-efficient technologies, smart building management, and advanced heating and cooling systems. The strategic location of Ostrov was also a decisive factor, as it brings ZF closer to Central and Eastern European markets, reducing transport distances and associated emissions.
“We are pleased to celebrate the completion of our new automated distribution centre in Ostrov, which stands as a testament to ZF’s commitment to pioneering mobility solutions and sustainable operations. Our close collaboration with Panattoni was key in transforming this brownfield site into a state-of-the-art logistics hub. Together, we have created a facility that will strengthen our logistics capabilities across Europe, ensuring we can supply our customers with automotive parts as quickly as possible,” said Klaus Heidrich, Executive of ZF Aftermarket Ostrov s.r.o.
Thanks to the modernization and optimization of logistics processes, the first phase of the 57,400-square-metre facility was equipped with 18 loading docks, which is 25% fewer than originally planned. This adjustment also eliminated the need for a loading yard along one side of the building, freeing up an additional 5,400 square metres of green space within the complex. The heating, cooling and ventilation systems in the facility are designed as a combined solution using heat pumps with ROOFTOP units (air-to-air systems using R32 refrigerant) and electric radiant panels for heating. The office spaces in the administrative building are heated and cooled by multi-split units, combined with electric convectors and heating mats. The new facility is not connected to any fossil fuel sources, positioning it to achieve one of the highest levels of the BREEAM New Construction international sustainability certification.
“Ostrov in the Karlovy Vary Region has a strong industrial tradition, which is now being successfully revitalized through the development of modern business infrastructure. ZF employs over 168,000 people worldwide, including more than 3,500 in the Czech Republic. We are pleased that this major employer has chosen to expand into Ostrov. The new ZF facility will not only create new jobs but also introduce a technologically advanced and innovative operation that will strengthen the competitiveness of the entire region. We highly value our collaboration and wish ZF great success in their new building,” added Martina Nová, Associate Director for Acquisitions and Project Management at Accolade Group.
“We are thrilled to be directly involved in the creation of an ultramodern and technologically advanced hub that is becoming an integral part of Ostrov’s growing industrial area. The shared services centre within the project has the potential to positively impact the education system in the Karlovy Vary Region. This new facility will undoubtedly contribute to the broader development of the locality. At the same time, it serves as a great example of effective brownfield redevelopment, as we managed to reuse nearly all construction waste from demolitions for further development,” said Klára Sobotková, Regional Development Director at Panattoni.
Transformation of a former trolleybus factory
The industrial park has been developed on the site of one of the largest brownfields in Czechia, which previously housed a trolleybus manufacturing plant. Originally constructed in the late 1950s, the factory produced up to 350 trolleybuses per year from 1960 onwards. However, as production was gradually relocated to Pilsen, operations ceased in 2004, leaving the site abandoned and deteriorating.
“In the 1950s and 1960s, there were many companies operating in Ostrov, initially linked to the uranium industry. Over time, however, the town became home to businesses mainly in the light industry sector, employing entire families from the local community. As the Mayor of Ostrov, I am pleased that a new modern industrial facility has been built on the site of the former trolleybus factory. This development brings new job opportunities for people, allowing them to work in a state-of-the-art environment with modern technologies. The development of Ostrov’s industrial zone is significant not only for our town but also for the Karlovy Vary Region, which is one of the structurally affected regions in the Czech Republic,” added Pavel Čekan, Mayor of Ostrov.
As part of the brownfield remediation, a total of 12,700 tonnes of hazardous waste were sorted and processed on the site for eco-friendly disposal according to its contamination type, preventing harmful substances from polluting the groundwater. In total, 98.7% of the original construction and demolition waste from the former complex was successfully recycled. This means that 103,000 tonnes of recycled material were used in the new construction, replacing primary raw materials. This approach eliminated the need for approximately 10,300 truck journeys, significantly reducing the environmental impact and minimizing disruption to the surrounding area.